- Dakota City, NE
- Contact: +1 (402) 987-3412
- sales@broyhill.com
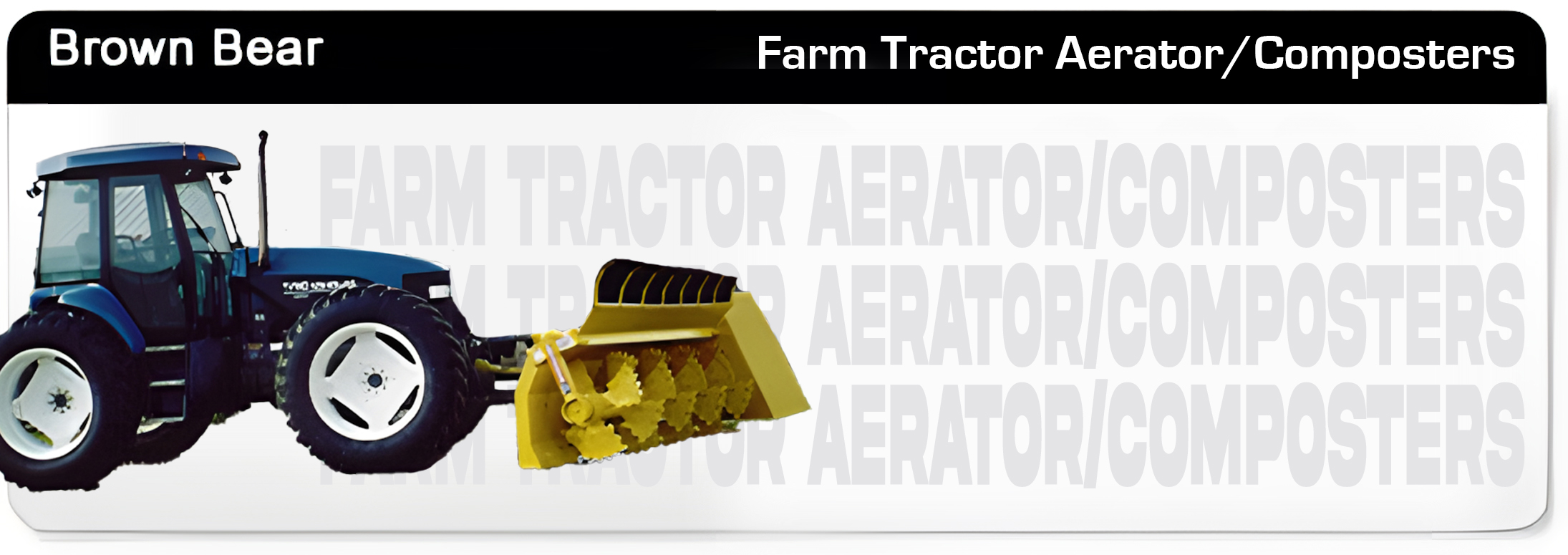
100-160 PTO hp tractors
Overview
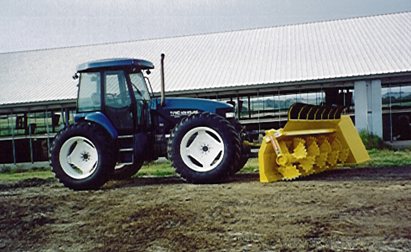
Brown Bear Corporation has introduced a revised model of its farm tractor composter. The PTO PTOPA35E-10.5 unit is designed to be attached to the front of 100-160 HP farm tractors. The composter requires a front 3-point hitch, 1000 RPM PTO, and creeper transmission. It is available for ISO and counter ISO PTO shaft rotation. Compost biosolids, yard waste, manure and other organics easily and inexpensively, as well as feedlot, dairy, poultry and swine manure. Composting assures CAFO and AFO compliance, as compost is exempt from the new proposed federal CAFO standards. Governmental loans and grants, such as “319 funds” may be available for equipment purchases used to meet the new CAFO regulations. Contact us for more information.
Key Service
- Largest capacity in its price class
- Front or rear mount to most tractors w/ CAT II or III 3Pt. Hitch
- Compost produces increased crop yields and soil water retention
- Composting eliminates flies and odors
- Composting produces dry granular product and reduces volume by 50%
- Affordable, easy to operate and inexpensive to maintain
30-60 PTO hp tractors
Overview
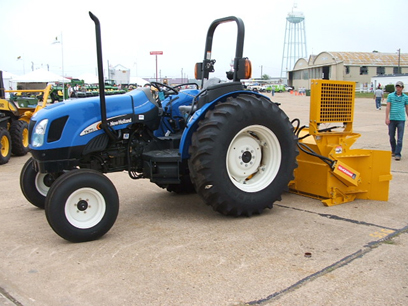
HYDPTO24
Mounting: Front or Rear CAT I 3-pt hitch
HP Requirements: 30-60 PTO, 540 or 1000 RPM,ISO or Counter ISO Rotation
Transmission: Hydrostatic,creeper,IVT or CVT recommended
Width: 7 or 8 foot width options
Options: Hydraulic Tilt,radiator pre-screen,fan reverser,cable guards
HYDPTOLM24 “Split System”
Mounting: Front bucket loader, CAT 1 3-pt hitch,or custom mount
HP Requirements: 30-60 PTO,540 or 1000 RPM,ISO or Counter ISO rotation
Transmission:Hydrostatic,creeper,IVT or CVT recommended
Width: 7 or 8 foot width options
Options: Hydraulic Tilt,radiator pre-screen,fan reverser,cable guards
Aerator is mounted on front 3-pt hitch or loader arms, reservoir, radiator, fan, gearbox and pump mounted on rear 3-pt hitch
Products
Explore our advanced solutions!
Ready to enhance your productivity with powertul and efficient equipment?
Poultry
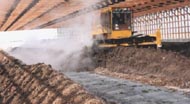
Model 400 w/standard 3 Pt. Hitch & 3940 Saw-tooth Paddle Aerator,
Composting Poultry Manure
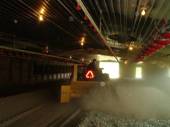
Broilers : TennesseeValley RC & D Decatur, Alabama
The Tennessee Valley RC&D utilized a US EPA grant to purchase four Brown Bear HYDPTO24-7′ compost aerators for installation on small farm tractors which will be loaned out to Broiler Growers in a four country area around Decatuar, AL. The local Soil and Water Conservation Districts will administer the loan out program. The growers raise broilers for four major Integrators in the area. Since broiler litter is a significant problem in land application due to high residual phosphorus levels in the local soils, a result of years of land application, the RC&D is looking at alternate methods to handle the litter. Using the Brown Bear attachment provides three major benefits which allow the litter to be reused again and again: sterilization of the litter through the composting process, decaking of the litter, and volatilization of the ammonia.
Layers: Heisler’s Egg Farm Inc. Tamaqua, Pennsylvania
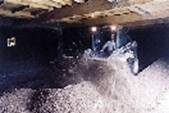
For the first time in its 40 years of operation, Heisler’s Egg Farm Inc., Tamaqua, Pennsylvania, has no fly problem. “After running the aerator through the accumulating manure about three times a week, we have reduced insect populations by better than 95%” states Todd Heisler. “When we’ve had the time to complete four or five cycles a week, we’ve reduced insect populations by better than 99%. Each turnover thoroughly mixes new manure with that already aerated. Heat builds, killing larvae, pathogens, and other undesirable pests. Oxygen penetrates all portions of the manure windrows, facilitating the desired natural low-odor aerobic digestion.” The compost which now results has proven to be a much better soil additive than the non-aerated manure previously produced. It is far more granular, easier to field-apply and, according to Jay Heisler, consistently increases yields of the crops we use it on corn, oats, and alfalfa hay.”
As to costs, reduction of insecticide applications, by itself, has paid for the auger attachment in a year. The farm uses their single skid loader to handle the Brown Bear aerator, a light-material bucket, an excavating bucket, and a set of forks for handling palletized boxes. Changeover between each front-end device takes a single operator less than 5 minutes. The benefits of using the Brown Bear aerator are abundant. “In addition to improving our working conditions, saving money and ending our fly problem, the Brown Bear auger sure helped improve our public relations” Todd Heisler concludes.
Baer Brothers Egg – Lake Park, Minnesota

Baer Brothers Egg at Lake Park, Minnesota implemented composting in order to achieve fly and odor control after years of complaints by neighbors. Their composting program eliminated the possibility of regulatory action by county and state agencies, and won them a Minnesota State Agriculture Environmental Achievement award.
Baer Bros. composts the manure from approximately 800,000 layers housed in natural convection high rise houses. The manure is removed weekly, inside the fly hatch cycle, and mixed with a variety of locally available carbon sources next to the high rise houses on concrete pads. The manure is turned here about two to three times the first week to kill the fly larvae. “The fly larvae crawl out to the outside of the windrow to avoid the 150 degree heat and then we turn the row to mix them back into the heat and kill them. We do this about one week, then we move the compost to our clay pad for final composting”, states Amon Baer, President. On the clay pad the windrows are aerated weekly and composting continues for about 90 days. Fresh manure is continually added for moisture and to increase the nutrient value of the compost, until the carbon is completely consumed. The final product is fly, odor and pathogen free and is certified as “Organic Fertilizer” The product is sold to local golf courses, organic dairy farms and farmers at the current values for N, P, and K which is about $38.00 per ton.
Mortality composting is also a part of the program. In an isolated windrow that is achieving good temperatures of 140-150 degrees, the top of the windrow is removed and the dead birds placed on the remaining base, after which they are recovered with the previously removed top. Within three days the birds have totally disintegrated and the windrow is aerated with the Brown Bear unit. Mortalities are added daily or as required.
Pullets: David Kneller Farms Silver Lake, Indiana
Dave Kneller, a contract pullet grower for a large egg producer in northern Indiana, raises approximately 115,000 pullets per cycle (the typical cycle lasts 16-18 weeks). Prior to using Brown Bear composters, Dave spent 1-2 hours per day spraying for flies at an annual cost of $7,000-$8,000. He noticed, however, that after a few months the flies became immune to the spray! Dave even faced a lawsuit from unhappy neighbors that threatened to shut down his operation. Then in November of 2002, Dave began using Brown Bear equipment, which solved his fly and odor problems. Within a few months of operation, the lawsuit was dropped. His neighbors have never been happier, and his integrator is very satisfied with the results. The Indiana Department of Environmental Management Regional inspector has also praised Dave’s new method of manure handling. Since starting his under house composting, Dave has reduced the volume of material he removes at clean-out time by 50% and has 99% complete fly control. Dave notes the added benefits of using the Brown Bear composters: the spreadability of material, the lack of rodents living in the manure, and reduced labor costs. His labor time has gone from 1-2 hours per day to 15 min every third day.
Beef
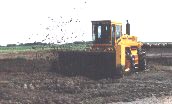
Adams Land & Cattle Co. – Broken Bow, NE
After seeing a demo, a Brown Bear 500 was immediately purchased and put to work drying the pens of Adams Land & Cattle Co. during “the wet spring of 93.” Adams Cattle Co. is also using their composted manure for fertilizer. “We’ll dry it from 80% moisture to 25% moisture, then spread it on our own agricultural land,” explains Gary Kenel, supervisor.
As with all cattle producers, Bill Adams is very concerned with his rate of gain. “Increased cattle comfort means increased gain. If they have to fight mud, it just eats you alive; it’s unbelievable. We’ve seen a 1/10 pound per day gain. You do all you can for cattle comfort because that will pay back to you in big dividends.”
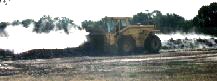
Double MM Farms – Kearney, NE
Double MM Farms has a small 2500 head commercial beef cattle feedlot and several thousand irrigated row crop acres. They have been using co-compost generated from the manure out of their feedlot and the waste water sludge from the nearby Kearney WWTP, to supplement commercial fertilizers on their crop acres. The manure and sludge is mixed, blended and composted by Mercers, using a Brown Bear I compost machine. The dry, granulated end product is spread on the farmland using a dry box spreader.
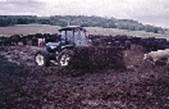
Cold Springs Dairy Farm – Hanover, IL
Maintaining milk production on a Midwest drylot dairy farm is very difficult during the muddy season when the combination of melting snow, ice and rain contribute to muddy lots, which in turn stresses the animals. Scraping the lots helps keep the cattle out of the mud, but creates masses of wet manure that crusts over and will not dry out in the pen. Hauling the manure out of the pen increases open pen space but creates a mass of non-drying manure that will not pile and covers many acres. To solve the problem, Cold Springs Dairy has started composting their piled manure with a Brown Bear PTOPA35-10.5 attachment on a New Holland TV-140 farm tractor. Composting reduces the volume by two-thirds and kills the seed germination and pathogens in the manure, making it more valuable for application back on their cropland (corn yields progressed from 80 bpa to an average of 180 bpa). The PTO auger aerator delivers a second major benefit in bed clearing – the consistent pickup of manure at its shear point with the clay below, which greatly reduced clay-replacement costs and improved overall cattle health and weight gains.
Cold Springs Dairy Farm’s success with the Brown Bear auger aerator spurred a veteran Illinois county agricultural agent to state, “The Brown Bear is the only aerator composter we know of that builds its own initial windrows. Since it always works directly in line with windrowed materials, it requires no alleyways. Existing space is better utilized, mixing is more thorough, and the compost produced is of very high quality. We feel confident in recommending this type of aerator compactor to all serious beef producers, small, mid-sized or big.”
Dairy
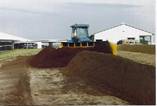
Prairieland Dairy, LLC Firth, NE
Co-Owner Dan Rice and the employees of Prairieland Dairy milk around 700 cows, three times a day. Operating what Rice calls a “enclosed system” Prairieland cleans their barns with recycled flushwater which runs to a separator. There the liquids are pumped to a lagoon and land-applied while the solids are piled for a week before being composted in windrows by a Brown Bear PTO-PA 35C auger aerator attached to a farm tractor. By turning the manure three times a week for six weeks, Rice is able to dry the 90% moisture manure into sanitary, 30% moisture compost that he uses for bedding thus completing his “enclosed system” In addition to cutting their bedding costs from $2,000/month for sawdust to $1,000/month to produce the composted bedding, Prairieland is selling about 25% of their compost to landscapers on the retail market for $25 per/yd, a nice profit from their $5 per/yd production cost. The compost has a 2:1:1 NPK rating and a 95% coliform kill rate. Rice has been able to cut the dairy’s somatic cell count in half (from 450,000 to 200,000), their lowest in three years.
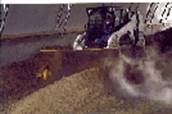
Northwest Missouri State University Laboratory & Research Center Maryville, MO
Dr. Dennis Padgett, a professor of agriculture at Northwest Missouri State University (NWMSU), is conducting exciting research in biofuels. NWMSU’s eighty cow dairy laboratory is transforming cow and pig manure into pelletized biofuel by drying the waste product with a Brown Bear 24 Series Paddle Aerator attached to a skid steer with high flow hydraulics. After flushing the parlor and going through a separator, the solids are composted and dried in a hoop shed from 90% to 35% moisture. In the hoop shed, the raw manure (90% moisture) is added to a windrow of dried compost (35% moisture) at a 1 to 3 ratio. A biodegradable bulking agent such as chopped corn and/or bean stalks is also added. Two passes with the Brown Bear aerator thoroughly blends and mixes the materials and builds one windrow. Through a process of airing and heat build up, the windrows dry to the desired 35% moisture in two days (being turned twice daily). From there the material is hauled to the university’s pellet mill where the compost is palletized and made ready for the power plant’s boilers where the manure becomes energy. The finished compost meets all CAFO regulations, so could be land-applied or sold on the compost market.
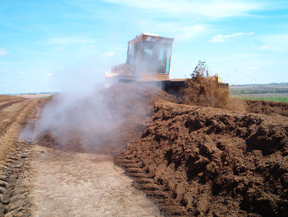
Milk Unlimited Atlantic, IA
Milk Unlimited, a 3800 head dairy, uses a Brown Bear Model 500 to compost 25,000 tons/yearly of manure for bedding. The manure comes off of a separator at about 30% solids and is taken directly to the compost site. Dr. Kelley Cunningham, the dairy’s manager, is now supplying half of his bedding from the compost over a 9 month period (he doesn’t compost during the winter months) at a cost savings of about $45,000 per year. He turns the compost for six weeks (5 to 6 hours per week) before returning the transformed material to the barns as bedding. He is working to double the amount of compost he produces in order to supply all of the bedding during the 9 months of composting for a savings of $90,000 per year. His windrow temperatures consistently run at 150 degrees F which provides good sterilization. He has had no increase in somatic cell count (SSC) since he started using composting for bedding.
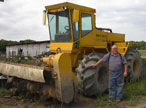
Bill McPhee Kindee, MI
William (Bill) McPhee raises 1800 replacement dairy heifers on his farm in Kindee, Michigan. Concerned with new CAFO regulations coming into effect in ’06, he purchased a used Brown Bear composting unit that he has been using for the past two seasons. Bill normally scrapes his stalls and stacks material in the winter from December to April. Then he uses the Brown Bear to tear down the piles and form them into windrows, which eliminates extra labor and equipment since the Brown Bear is the only machine available that builds its own initial windrows. He actively composts from April to very late November when the weather gets too cold for the windrows to retain high temperatures. There is no carbon added to the mix except the small amount of bedding that comes with the manure. Composting reduces the material’s volume by 50%. Average precipitation in this area off Lake Huron is 16″ of rainfall and 24″ of snowfall annually. Bill is currently enrolling in the MEAP program in Michigan which requires him to have zero run-off and makes his facility exempt from federal CAFO regulations.
Why Choose Us
Industry-Leading Technology
By choosing Brown Bear, you gain access to industry-leading technology that enhances productivity, reduces operating costs, and ensures compliance with environmental regulations. Our equipment not only improves efficiency but also promotes sustainability in your operations.
Proven Expertise:
Brown Bear Corporation specializes in manufacturing high-quality equipment for composting, sludge drying, and utility tasks, ensuring reliable performance and industry compliance.
Innovative Solutions:
With a diverse product line includes advanced brush mulchers, composters, and bioremediation equipment, designed to enhance operational efficiency and reduce environmental impact in various sectors.
Customizable Equipment:
Brown Bear offers tailored solutions with options for different tractor types and attachments, allowing customers to find the perfect fit for their specific needs and maximize productivity.
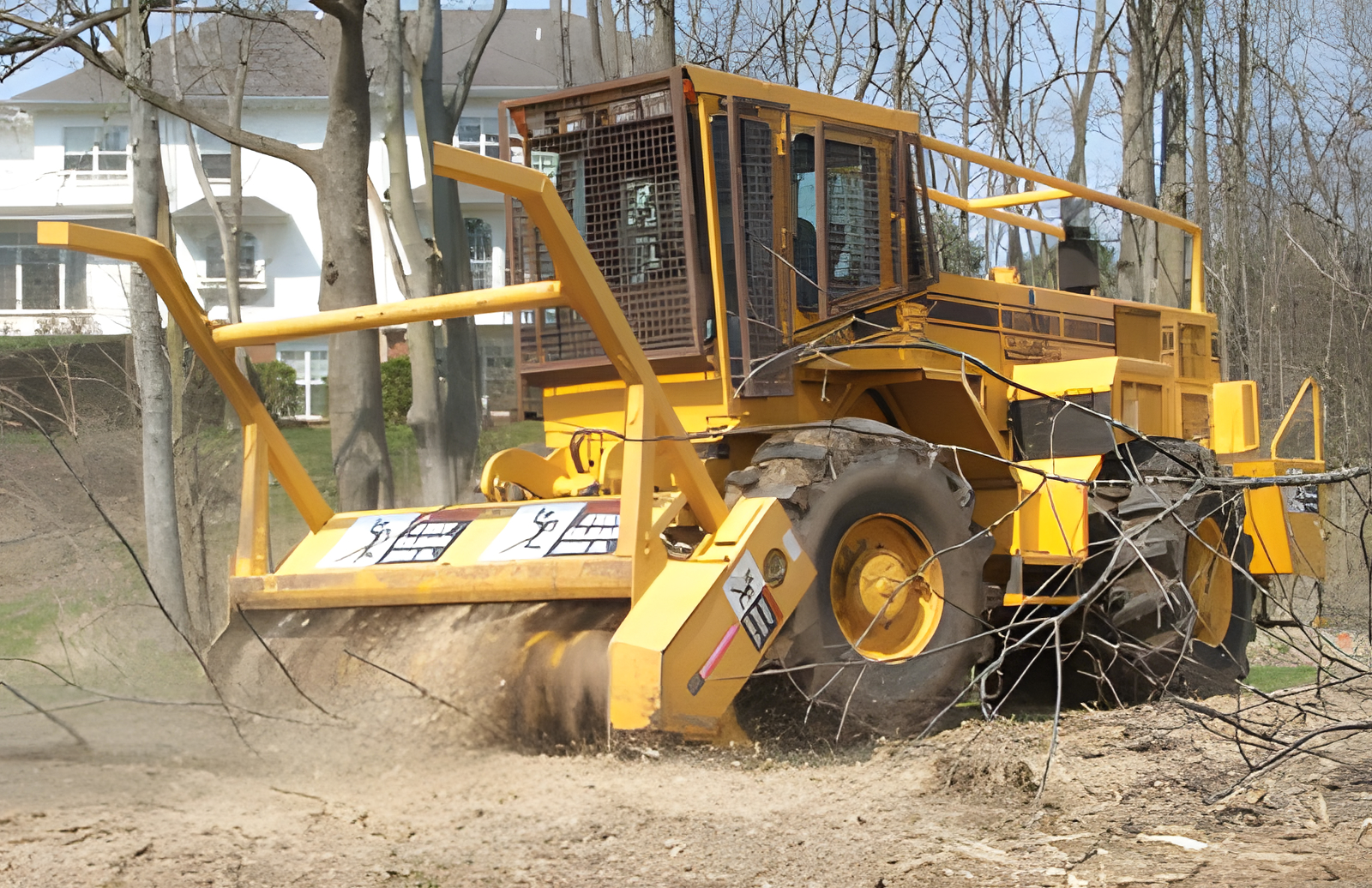
Testimonials
Words of Appreciation from Our Valued Clients
At Brown Bear, we take pride in delivering high-quality equipment that meets the diverse needs of our customers in agriculture, utility, and environmental sectors.
But don’t just take our word for it—hear from those who have experienced the benefits of our products firsthand!
Our customers consistently share their success stories, highlighting how our innovative solutions have transformed their operations, improved efficiency, and enhanced sustainability. From composting and waste management to brush cutting and land clearing, our equipment is designed to deliver exceptional performance and reliability.
Explore the testimonials below to see how Brown Bear equipment has made a positive impact on businesses like yours. Join our community of satisfied customers and discover how we can help you achieve your goals!
Using my Brown Bear composting unit has transformed my operation. It builds its own windrows, cutting down on labor and reducing material volume by 50%. I couldn’t be happier!

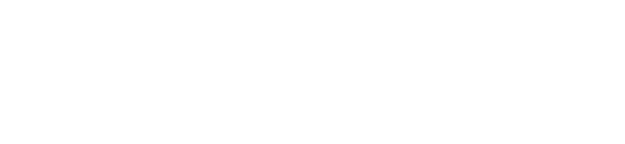
At Brown Bear, our mission is to provide innovative, high-quality equipment solutions that enhance environmental sustainability and operational efficiency across the agricultural, utility, and pipeline industries.
Products
Information
© 2025 All Rights Reserved by Brown Bear